Paladin79
Previously MOT: Cables For Less
This is my "I have 15 minutes to accomplish this the ball game is about to start" dual 3 pin male xlr to single 4 pin female xlr conversion. It will be easier to just build cables to four pin XLR males than some to that and some to dual 3 pin xlrs. Please note I have all supplies at hand and have memorized xlr layouts so it was a quick build. Inside the four pin xlr I marked each pair with red or black heat shrink tubing to be able to quickly tell them apart. I used Mogami star quad and Neutrik connectors. The amps are dual NuForce HA-200's with enough power to push any headphones I own.
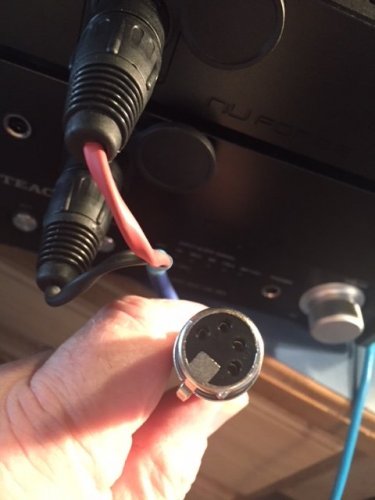
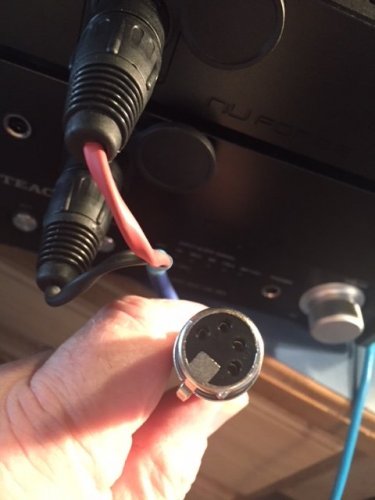