MikeJSmith
Head-Fier
- Joined
- Dec 30, 2015
- Posts
- 81
- Likes
- 51
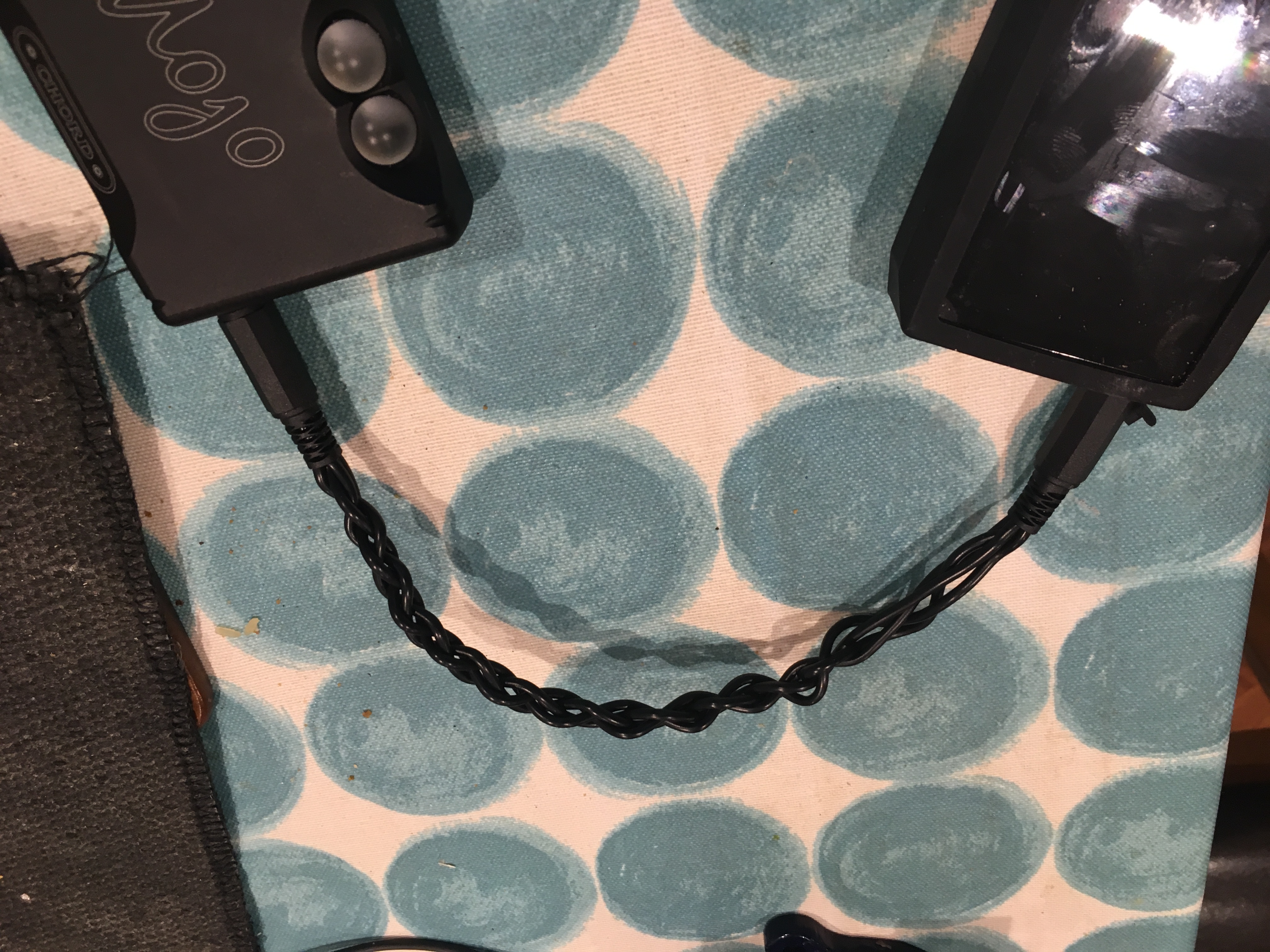
they are not braided in the original jacket; they are twisted, but twisted very well.
It's insulation between the wires and plug.So, I'm about to attempt my first custom cable build. The plan is for a 5' TRS cable for my Audeze cans. I'm using 24 awg wire from BTG and it will be braided and then inserted into paracord 550. At the split, the two Y ends will be twisted and then each twisted pair will be inserted in paracord 95.
I'm a newb at this and could use some clarification on a few simple things.
1. I have a Rean TRS jack that came with a roughly 1" long clear plastic thingy. Is it supposed to be a strain relief, or clear shrink tubing? If shrink tubing, should it be shrunk over the wires completely inside the rear part of the connector, or some of it be visible sticking out the back when I'm done?
![]()
2. The 550 paracord is awfully small diameter for the connector's exit point, isn't it? Is this a concern? Is it going to get much bigger with 4x24awg wires braided inside it? It looks kinda funny this way.
![]()
3. I'm not quite certain how to wire this baby up. Of the two obvious connection points, which one is the tip and which is the ring? And where does the sleeve wire get soldered to? Are those two rear tabs just for clamping the wires in place after soldering? There's also a thin piece of material that I assume is an insulator.
![]()
@Little Bear , sorry forgot to answer your other questions and concerns.
two 24AWG wires twisted together will not likely fit into 95lb paracord. Certainly you can try, but one 24AWG is a tight fit.
If you are going to make cables, get a multimeter. Any cheap one is fine. You just need to be able to check for continuity, which allows you to determine what is connected to what. I wrote up a little set of instructions here. Once you have a multimeter, you can determine which solder lug is tip and ring. Until then, the smaller one is tip, and the bent one is ring.
The black part unscrews.
How hard is it to unscrew? I tried but it didn't give easily.
EDIT: The black outer cover does not unscrew.
Yeah it looks like the strain relief unscrews from the back but it appears the part with the contacts may just push out from front to back. Go here and take the link for the pdf assembly info on the upper right part of the page:
http://www.rean-connectors.com/en/products/tiny-xlr-cable-connectors/rt4fc-b
![]()