You are using an out of date browser. It may not display this or other websites correctly.
You should upgrade or use an alternative browser.
You should upgrade or use an alternative browser.
"Open Alpha" T50 3D printed headphone project from MrSpeakers
- Thread starter mrspeakers
- Start date
That’s a good idea mate.Sure, without a doubt.
The thin kapton film is very sensitiv, thats why i‘ve used some thin electric tape which i wrapped around the frame. So if you accidentally pull on the wires, it should´nt do any damage.
![]()
It’s almost like these drivers have been purposely designed to break if anyone dares to tinker with them.
socks2sound
Head-Fier
- Joined
- Jun 24, 2012
- Posts
- 73
- Likes
- 28
https://www.reddit.com/r/headphones/comments/qk96i8/got_inspired_by_the_fostex_th900_series_and/@socks2sound that looks amazing. I'd love to know the finishing process
I explained it here lol
SeEnCreaTive
500+ Head-Fier
- Joined
- Oct 6, 2014
- Posts
- 667
- Likes
- 269
Hah, oh my, that is quite the job, I think I might have to personally skip trying that
Excellent work
Guys has anyone successfully printed these on an SLA printer? Im very new to resin printing and have some questions.
Got mine done as well
Thanks @IvanDrago and @SeEnCreaTive for your help.
I've been tuning for some time now and had to fight a bit to contain the high notes, but I'm really happy with them overall.

I've been tuning for some time now and had to fight a bit to contain the high notes, but I'm really happy with them overall.
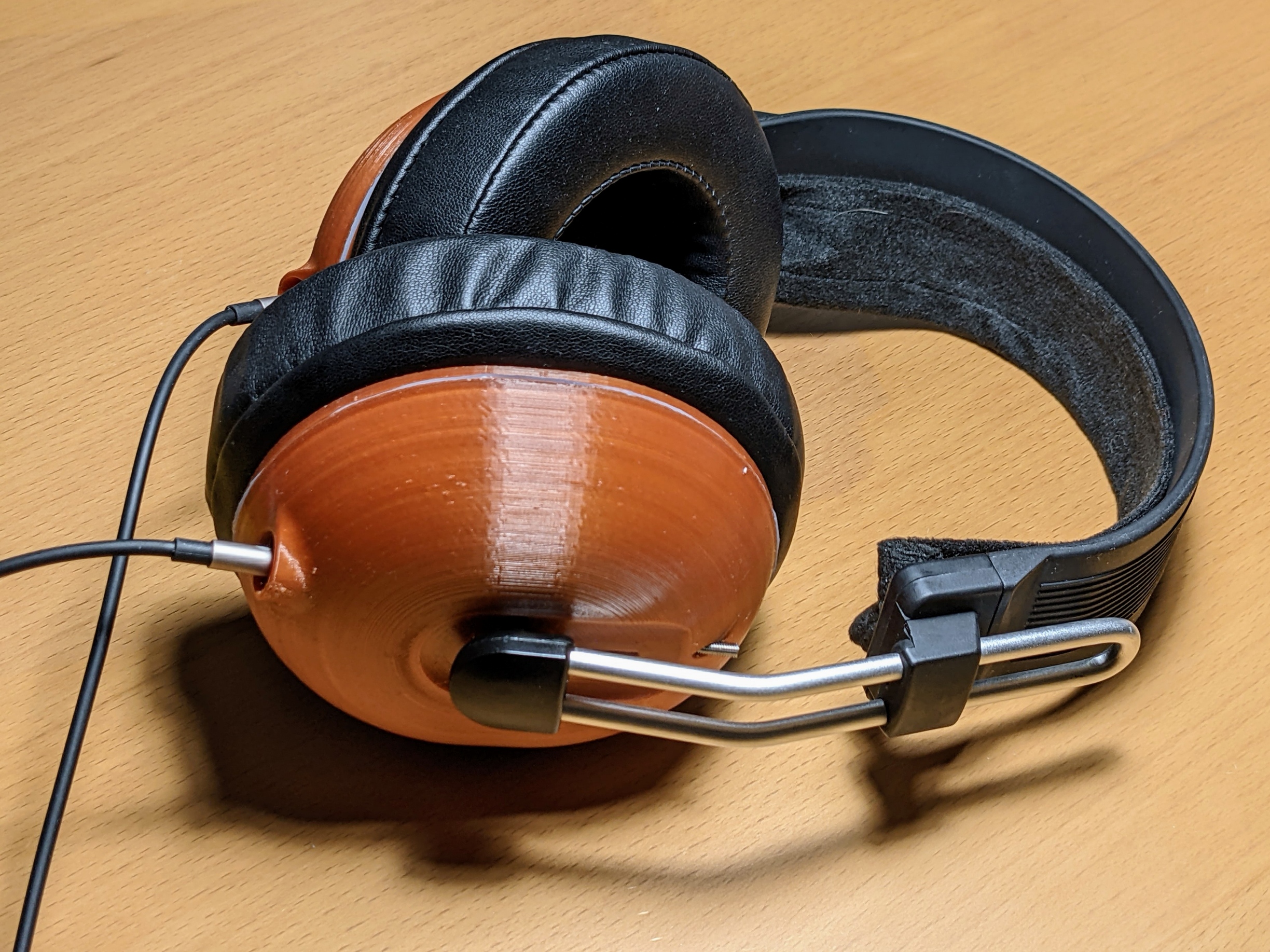
SeEnCreaTive
500+ Head-Fier
- Joined
- Oct 6, 2014
- Posts
- 667
- Likes
- 269
Got mine done as wellThanks @IvanDrago and @SeEnCreaTive for your help.
I've been tuning for some time now and had to fight a bit to contain the high notes, but I'm really happy with them overall.
![]()
Of course! The fun of T50rp modding is seeing all the people trying it
DCA used to use "dog treats" back in the Alpha Dog days. From what I can tell, bits of Paxmate stuck to the ear side of the driver to help tame the highs
Does anyone know where I can buy the connectors for this? I printed out the cups and ear pad rings with wood PLA, but unfortunately I need to wait on a new nozzle as it got clogged. I'll finish the baffles when I get new parts for the 3D printer. It's ok, lots of sanding and priming to do in the meantime
I'd actually like to use 3.5mm or 2.5mm connectors if I could...I don't know if they would fit in there or not though...But I'd need to get a new cable otherwise.

I'd actually like to use 3.5mm or 2.5mm connectors if I could...I don't know if they would fit in there or not though...But I'd need to get a new cable otherwise.
Use this one.I'd actually like to use 3.5mm or 2.5mm connectors if I could.
https://www.thingiverse.com/thing:2326371
Last edited:
Aw man, have to print new cups now ha. Thanks though. I wonder if there's any way to fit connectors in the original design.
Maybe you could print an adapter and use some superglue.I wonder if there's any way to fit connectors in the original design.
Or buy the Hirose adapters+connectors
HR10A-7P-4P (73)
HR10A-7R-4S (73)
The originals are expensive but worth every penny. Cheaper ones could be found on Aliexpress. Quality is also good, but not on par with the originals.
CptSoftBelly
New Head-Fier
I'm having a tough time finding symettrical m2.5 threaded inserts in the us. I can find m2 and m3, this is irritating.Here are the stl files for heated inserts guys:
Exactly as stock except using a 3.5mm connector, and implementing heated inserts obviously..
https://www.dropbox.com/sh/ddzghyfh2r1nj1k/AABnAwMfcxCW52jYTvR4MSwSa?dl=1
Ive included an stl for the front slider cover, as I managed to strip the thread from my original ones, so might come in useful to someone.
Inserting heated inserts into the cups for beginners: (skip this part if you know what you're doing here)
So I've used 2 different heated inserts on my build, these ones are highly recommended for inserting into the cup as they take a ridiculous amount of force to pull out:
https://www.amazon.co.uk/gp/product/B07PP2SDST/ref=ppx_yo_dt_b_asin_title_o09_s00?ie=UTF8&th=1
I used an old soldering iron (set to around 230) which did the job fine, I know there are special tools and soldering iron bits available for doing this, but I had no problem with an iron.
My method for the cup inserts is to have a perfectly flat piece of metal on a hard surface nearby, then one insert at a time, (if you're using the inserts I've linked to then they should sit nicely in the cup hole), gently place the soldering iron tip into the insert from directly above, dont push down, just use the weight of the soldering iron...when the insert is about 80% submerged quickly put the iron down and flip the cup onto the hard flat surface and push down hard, there will be enough heat to finish the insert and the result will be a perfectly straight, perfectly flush insert.
Inserting heated inserts into the baffle:
These are cheaper ones that are fine for mounting the ring to the baffle, as they are inserted from the cup side of the baffle:
https://www.amazon.co.uk/gp/product/B08H563S9W/ref=ppx_yo_dt_b_asin_title_o02_s00?ie=UTF8&psc=1
Use the same approach to inserting the baffle inserts as above, but because the surface of the baffle isn't flat, instead of flipping over onto a flat surface to finish the insert off, just have a small flat metal object to hand to finish the insert off when it is 80% submerged, again this ensures a straight, flush insert.
I had this set lying around so you dont need all of them, just the M2.5x3.5x3mm ones...remember these need to be mounted from the rear of the baffle, after you have inserted them let them cool down for a few minutes, and before doing anything slowly screw a longer 2.5mm screw all the way through from the same side you inserted them. This will push out any filament that might be blocking the insert and the hole when you mount the baffle.
The screws I have are from this set:
https://www.amazon.co.uk/gp/product/B075WY5367/ref=ppx_yo_dt_b_asin_title_o06_s00?ie=UTF8&psc=1
The screws used for mounting the ring to the baffle are M2.5x8mm
The screws used for mounting baffle to the cups are M2.5x6mm
All screws should be fitted with a M2.5x6x0.5mm washer, I can't link to the washers as I have an old selection box full of them and I have no idea where they came from.
Be careful if not using these exact screw lengths as you could screw straight through the cup.
As far as tightening goes, personally I keep screwing until I start to feel resistance, and then do a quarter turn more. Obviously it would still be possible to over tighten these, because you'll just start to crush the 3d material you used to print.
I felt it best to leave the driver mounting as normal, as without modifying the drivers themselves I couldn't see a way to improve this, so mount the driver to the baffle exactly as per the initial instructions.
Personally I've cut reusable silicone gaskets that sit between the ring and the baffle, and between the baffle and cup, if you dont go down this route then obviously seal/glue these parts as per the initial instructions.
Any questions then just ask, any improvements or suggestions are welcome.
Good Luck !
Edit: Sorry I should point out, in your 3d printers settings, set perimeters to greater than 2, I've set mine to 4 for extra strength around the inserts.
TheFlash93
New Head-Fier
- Joined
- Oct 16, 2012
- Posts
- 35
- Likes
- 10
Does anyone have a most current part number from McMaster-Carr for the 4 screws to secure the baffle assembly to the cup?
Also sorry to necro post.
Also sorry to necro post.
socks2sound
Head-Fier
- Joined
- Jun 24, 2012
- Posts
- 73
- Likes
- 28
You can reuse the fostex screws, no need to buy more. The bass screw, I've found, is a perfect fit with 2mm instead 2.5mm.Does anyone have a most current part number from McMaster-Carr for the 4 screws to secure the baffle assembly to the cup?
Also sorry to necro post.
socks2sound
Head-Fier
- Joined
- Jun 24, 2012
- Posts
- 73
- Likes
- 28
I realize that it's been a while but is there a version where there's a bass screw and hirose connectors?Here are the stl files for heated inserts guys:
Exactly as stock except using a 3.5mm connector, and implementing heated inserts obviously..
https://www.dropbox.com/sh/ddzghyfh2r1nj1k/AABnAwMfcxCW52jYTvR4MSwSa?dl=1
Ive included an stl for the front slider cover, as I managed to strip the thread from my original ones, so might come in useful to someone.
Inserting heated inserts into the cups for beginners: (skip this part if you know what you're doing here)
So I've used 2 different heated inserts on my build, these ones are highly recommended for inserting into the cup as they take a ridiculous amount of force to pull out:
https://www.amazon.co.uk/gp/product/B07PP2SDST/ref=ppx_yo_dt_b_asin_title_o09_s00?ie=UTF8&th=1
I used an old soldering iron (set to around 230) which did the job fine, I know there are special tools and soldering iron bits available for doing this, but I had no problem with an iron.
My method for the cup inserts is to have a perfectly flat piece of metal on a hard surface nearby, then one insert at a time, (if you're using the inserts I've linked to then they should sit nicely in the cup hole), gently place the soldering iron tip into the insert from directly above, dont push down, just use the weight of the soldering iron...when the insert is about 80% submerged quickly put the iron down and flip the cup onto the hard flat surface and push down hard, there will be enough heat to finish the insert and the result will be a perfectly straight, perfectly flush insert.
Inserting heated inserts into the baffle:
These are cheaper ones that are fine for mounting the ring to the baffle, as they are inserted from the cup side of the baffle:
https://www.amazon.co.uk/gp/product/B08H563S9W/ref=ppx_yo_dt_b_asin_title_o02_s00?ie=UTF8&psc=1
Use the same approach to inserting the baffle inserts as above, but because the surface of the baffle isn't flat, instead of flipping over onto a flat surface to finish the insert off, just have a small flat metal object to hand to finish the insert off when it is 80% submerged, again this ensures a straight, flush insert.
I had this set lying around so you dont need all of them, just the M2.5x3.5x3mm ones...remember these need to be mounted from the rear of the baffle, after you have inserted them let them cool down for a few minutes, and before doing anything slowly screw a longer 2.5mm screw all the way through from the same side you inserted them. This will push out any filament that might be blocking the insert and the hole when you mount the baffle.
The screws I have are from this set:
https://www.amazon.co.uk/gp/product/B075WY5367/ref=ppx_yo_dt_b_asin_title_o06_s00?ie=UTF8&psc=1
The screws used for mounting the ring to the baffle are M2.5x8mm
The screws used for mounting baffle to the cups are M2.5x6mm
All screws should be fitted with a M2.5x6x0.5mm washer, I can't link to the washers as I have an old selection box full of them and I have no idea where they came from.
Be careful if not using these exact screw lengths as you could screw straight through the cup.
As far as tightening goes, personally I keep screwing until I start to feel resistance, and then do a quarter turn more. Obviously it would still be possible to over tighten these, because you'll just start to crush the 3d material you used to print.
I felt it best to leave the driver mounting as normal, as without modifying the drivers themselves I couldn't see a way to improve this, so mount the driver to the baffle exactly as per the initial instructions.
Personally I've cut reusable silicone gaskets that sit between the ring and the baffle, and between the baffle and cup, if you dont go down this route then obviously seal/glue these parts as per the initial instructions.
Any questions then just ask, any improvements or suggestions are welcome.
Good Luck !
Edit: Sorry I should point out, in your 3d printers settings, set perimeters to greater than 2, I've set mine to 4 for extra strength around the inserts.
Users who are viewing this thread
Total: 5 (members: 0, guests: 5)