Slater
Headphoneus Supremus
I have warned anyone I could about that issue in the past. I hope your experience will serve as a lesson for new comers too. Thanks for the heads up and sorry for your loss.
I'm back, with a new iMM-6 microphone. But this time I reinforced it so it is impossible to fall apart at the tip.
I wanted to share how I did it, as I know many others use the iMM-6.
The body of the iMM-6 is made of rubbery plastic (or is it plasticy rubber lol). But the cap at the end (that holds the microphone capsule) is aluminum. The only thing holding it on is glue. While this is fine for open air measurements, there is a high risk of the cap separating from the rubber body when repeatedly inserting and removing the iMM-6 in various couplings for FR measurement.
The basic idea is to insert (2) small screws, mechanically binding the aluminum cap to the body. This way, the risk of ripping the cap from the microphone body is eliminated when you push/pull/twist the microphone to insert/remove it in and out of couplers.
You'll need to find some small screws - I'm talking ridiculously small screws. Like the ones that are commonly used with various laptops components. They are generally around 1.25mm-1.5mm in diameter. The difference is the laptop ones are usually machine thread - you want non-machine thread (like the threads of a wood screw or drywall screw).
I used recycled screws (whenever I have electronics that go bad, I try and salvage anything of use from them (li-ion batteries, LEDs, electrical components, etc). I have a collection of hundreds of various ridiculously-tiny screws, nuts, bolts, etc - they take up hardly any room, and are useful for many projects like this (I keep them all in an empty pill bottle). If you don't have anything like that, I'm sure you can buy screws on Aliexpress (look for M1.25 or M1.5 screws, but make sure they're not machine thread).
The LENGTH is the critical part. They MUST between 2mm-2.25mm in length. Any longer, and you will damage the wiring. The absolute longest they can be is 2.5mm, so that's why I say 2.25mm max. That gives you a 0.25mm margin of error on each side (which is not very much, but if you follow my directions it will be perfectly fine). If you need to shorten your screws, do so (I had to shorten mine, because they were 3mm long). I just cut them down using wire cutters, and sanded the end smooth using a Dremel tool sanding drum.
So to get an idea of where we will be adding the screws, I'll show you what we're dealing with by showing my 1st iMM-6 that ripped apart. See the area by the wires? See how it's encased in a section of solid rubbery plastic? This is where we are going to insert the screws. The key is going deep enough to sufficiently bite into the iMM-6 body, but not deep enough to cut into the wires.
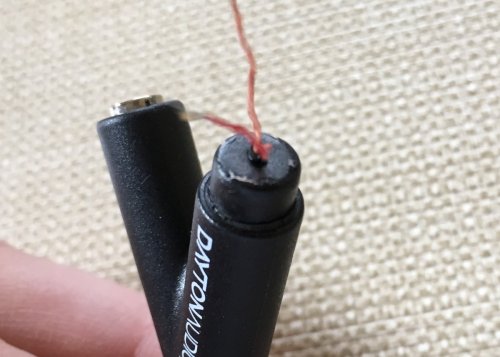
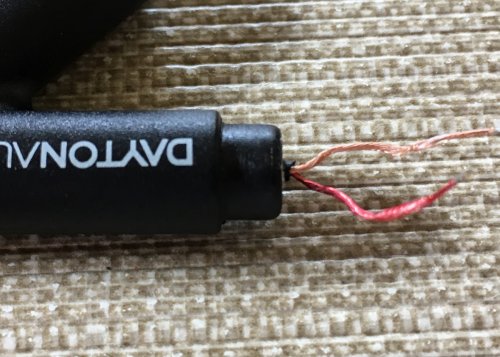
You also need some micro drill bits. You can order them on Aliexpress for about $2/set. I have an assorted set of carbide micro bits that range in size (graduated from 0.3mm to 1.2mm). Alternatively, if you own a Dremel tool, you may already have similar drill bits (if not, you can buy an assortment set made by Dremel as well).
You need to drill a hole through the thin aluminum cap ONLY, using a bit that is barely larger than the diameter of your screw shaft. So for example, if your screw has a 1.5mm diameter, make the hole in the aluminum cap 1.75 mm. Be sure you don't drill into the rubber body - your objective is to only pierce through the aluminum cap.
Also, you will be drilling all holes by hand. Use a twist drill mandrel for the drilling (you can buy on Aliexpress for a dollar or so). If your drill bits are sharp enough, and you go slow enough, this will only take a few seconds of twisting per hole.
Here is what a twist drill mandrel looks like (also called a twist drill pin vice):
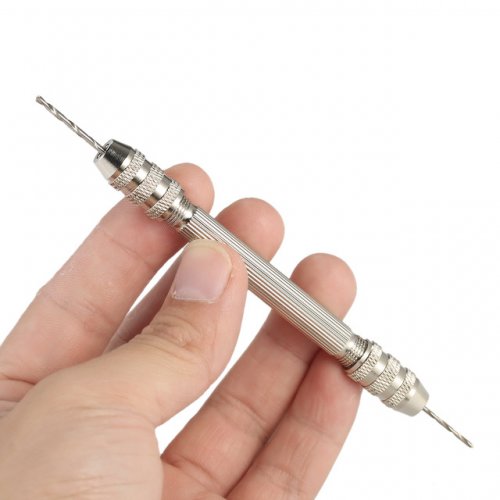
Here's a link to one that includes the pin vice and micro drill bits: https://www.aliexpress.com/item/Min...teel-Drill-Bit-Holder-Double/32818707913.html
You'll be making (2) holes in the aluminum cap - 1 on each side (ie 180 degrees opposite to one another).
Once you have made your small hole in the aluminum cap, use a SMALLER drill bit to drill a very small pilot hole into the rubber body. Again, I used my twist drill mandrel for this, and only drilled into the rubber body 2mm max. As far as drill bit diamater, if for example your screw has a 1.5mm diameter, use a 1mm drill to make the pilot hole in the rubber body. This will give plenty of rubber for the screws to bite into and secure the cap nice and tight.
Once you have all of your holes, it's a simple matter of inserting the screws and gently tightening them (you can use a drop of loctite or super glue as extra measure if you wish, but I found it unnecessary). If you over tighten the screws however, you will strip the fragile rubber and you are screwed (no pun intended).
Here is the finished product (on the new iMM-6, not the ripped apart one). It should be bulletproof now

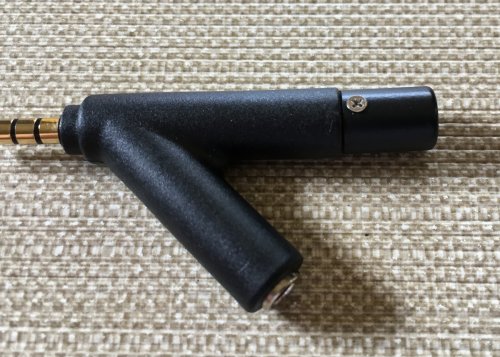
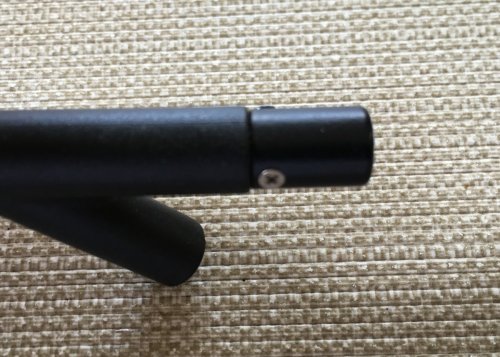
If you attempt this, you do it at you own risk. I'm not trying to scare you, as it worked perfectly fine for me. But if you use screws that are big or too long, drill into the rubber body deeper than 2.5mm, or use anything over than your hands, overtighten the screws, etc I cannot be to blame.
But learn from my exprerience (and others). I'm out $25 for the 1st destroyed mic, and another $25 for the replacement mic. Spend a few dollars and a few minutes of your time and protect your investment.
Last edited: