tomb
Member of the Trade: Beezar.com
- Joined
- Mar 1, 2006
- Posts
- 10,891
- Likes
- 1,066
While casework assembly has begun in earnest, I'd like to take a small pause to thank our suppliers. Of course, the main person to thank for the casework and its design is dsavitsk:
Dsavitsk does all woodwork on his own. For the metal casework, however, he uses Front Panel Express. FPE is familiar to almost all of the DIY-ers in the audiophile culture. They are known for great precision and quality. I've used them on a number of occasions myself and can absolutely confirm this. Plus, their Front Panel Design software (free!) is a top-notch way to design casework and specify how to cut, punch, machine and finish the metal. If any of you have need for a unique casework design that can't be met by the stock Hammond, Lansing, Box Enclosures, Context, etc. - FPE is a great choice.
There are some drawbacks with FPE, however, when it related to the T4:
As it turned out, Dsavitsk would have the metal cut at FPE, then send it out to a friend who would brush finish and then anodize. When he received it back, Dsavitsk would add the laser etching himself. This was not possible for me. So, I started searching. I figured that Atlanta was a large enough city that we should have similar services to FPE somewhere. I had already been using a local anodizer and laser etcher for many years that did world-class quality work. (I have experience with an anodizer who did not!) Both had done excellent work previously on Beezar Audio's DoodleBug, among other products:
That anodizing is provided by Metal Finishers of Atlanta. The laser-etching is provided by Laser Tech Atlanta. Both firms have done excellent work for me for almost a decade, now. I used to live only a couple of miles from Metal Finishers of Atlanta, so it was very, very convenient. Both services are true crafts, almost artwork. If you look at Laser Tech Atlanta's website, you'll see some fine examples of actual art and why I say that:
Anodizing is similar: the process is well known and documented, but the actual process details are more experience and judgment than anything else. The type of metal cleaning used, the method of clamping/mounting, and how long to leave the article in each tank during the process, are all variable tasks that can result in huge differences in quality.
Similarly, laser etching not only involves preparation of the artwork, but knowing the various materials and finishes and how to vary the etching settings variables that are necessary to have a design "pop" from the overall finish. It even takes first hand knowledge and experience of the anodizer in the depth of anodizing, etc. Most important - anodizing can actually be done over if it turns out bad, but laser etching cannot. It essentially ruins the metal, if it's not done right. When you've invested several $ thousands in the metal work, failures in anodizing or laser etching are not desirable prospects - to say the least! (I've had it happen, unfortunately!!)
So, all that was in my mind while searching for a solution for the metal. I had to find someone who could precision cut, punch, and brush-finish aluminum to an equal quality of Front Panel Express. Then, I'd have to have it anodized and laser-etched, but at least with those two services - I already had the solution.
After flirting with a number of machinists (my own ignorance), one of them said what I really needed was sheet metal work. Having been familiar with the HVAC industry for many years, "sheet metal work" meant bending thin gauge galvanized steel and assembling it into ductwork with very rough, self-tapping screws:
No! That isn't what I wanted. Yet, another machinist I contacted persisted: he said I needed to look at Swift Atlanta. So, I did.
The first thing I did was call them up and ask if they could machine metal plate and also brush-finish it. By that time, I had actually looked up the actual machines used to brush-finish (Time-Saver) and asked them if they had them - they did! Next thing I knew, they had invited me to their factory for a tour! Even though I had worked for Lockheed in my early career for 15 years, I was impressed with their operation! Giant Mitsubishi laser cutters, presses, Time Saver belt sanders (brush-finishers), CNC press brakes, etc., etc. They did clear anodizing and silk-screening (as good as I've ever seen), but no black anodizing or laser etching. I asked what they did if someone wanted black anodizing and laser-etching: their reply was that they used Metal Finishers of Atlanta and Laser Tech Atlanta! The same people I used! They also stated that they'd handle the entire operation and quality control - including the outside services!
Speaking of the HVAC industry, Swift Atlanta does all of Automated Logic's casework:
That's not exactly the style of casework we wanted for the T4, but you can see the quality workmanship, regardless.
I had several more meetings with them, showing them the T4 finished prototype and letting them have a look at it, while I produced an entire set of CAD drawings for them. This was a lot of work. Dsavitsk had done the initial work in Front Panel Designer for FPE, but as convenient as their software was, it was not commercial/industrial CAD. I had done this in the past with Lansing on the Millett MiniMAX, Hammond Mfg with the Starving Student, PupDAC, and DoodleBug, and with Context Engineering on the original Torpedo. So while a lot of work, it was something I had done before. Here's a couple of examples of the drawings that I produced:
Please remember - I can't take credit for the design! This is Dsavitsk and ECP Audio's creation! I like to think my contribution was definitely value-added, however.
Anyway - I highly recommend Swift Atlanta (and the other two processors) for anyone interested in some high-level casework. My experience with Swift Atlanta was one of the nicest - if not THE nicest - I've ever had with a supplier. They even sent me a Christmas card:
Great people! I just thought some of you would like to know the many people who helped make the T4 possible. It's not just me and Dsavitsk!
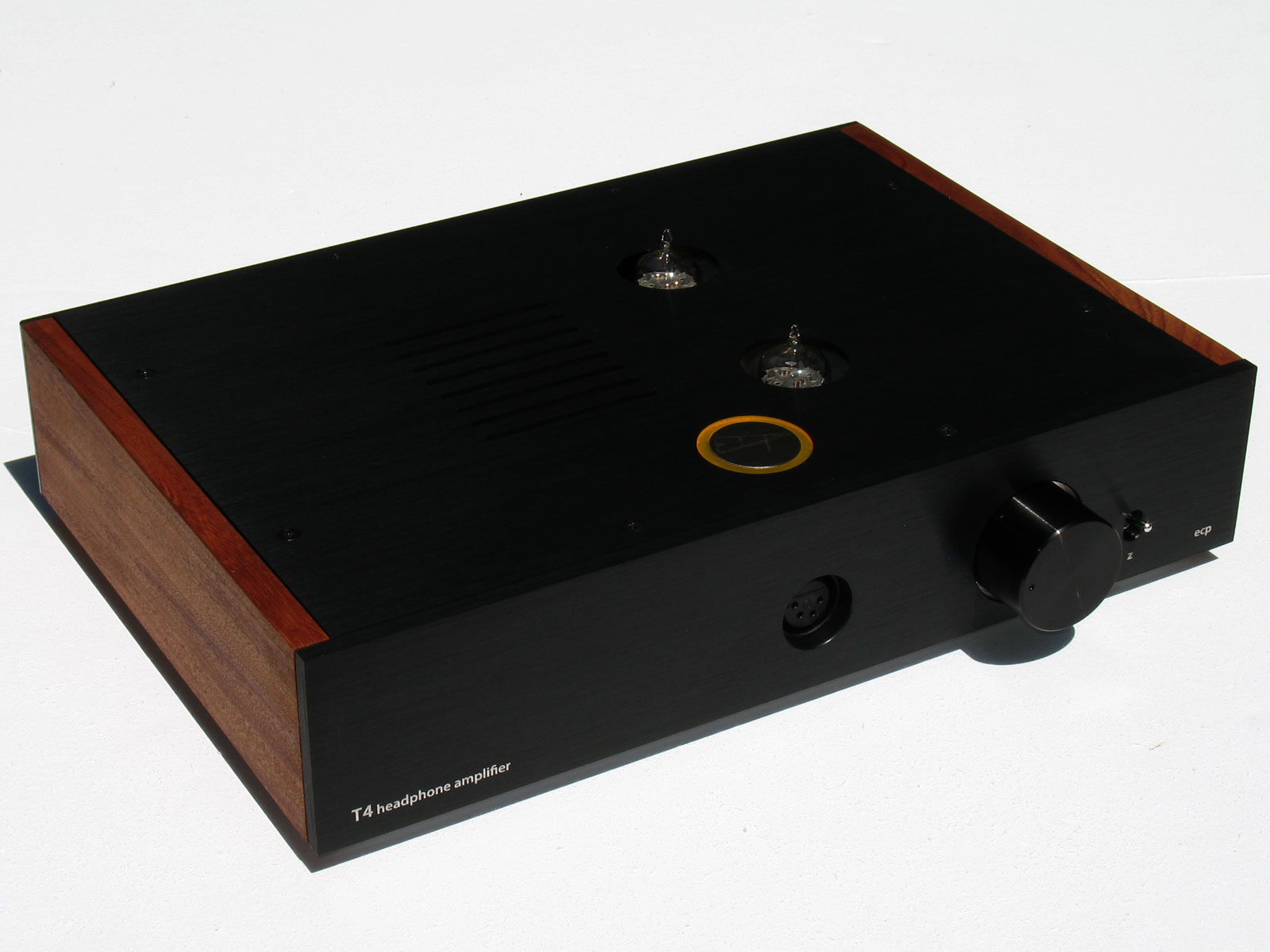
Dsavitsk does all woodwork on his own. For the metal casework, however, he uses Front Panel Express. FPE is familiar to almost all of the DIY-ers in the audiophile culture. They are known for great precision and quality. I've used them on a number of occasions myself and can absolutely confirm this. Plus, their Front Panel Design software (free!) is a top-notch way to design casework and specify how to cut, punch, machine and finish the metal. If any of you have need for a unique casework design that can't be met by the stock Hammond, Lansing, Box Enclosures, Context, etc. - FPE is a great choice.
There are some drawbacks with FPE, however, when it related to the T4:
- No brush finish capability,
- No anodizing after machining, and
- No laser etching (engraving or UV inking instead).
As it turned out, Dsavitsk would have the metal cut at FPE, then send it out to a friend who would brush finish and then anodize. When he received it back, Dsavitsk would add the laser etching himself. This was not possible for me. So, I started searching. I figured that Atlanta was a large enough city that we should have similar services to FPE somewhere. I had already been using a local anodizer and laser etcher for many years that did world-class quality work. (I have experience with an anodizer who did not!) Both had done excellent work previously on Beezar Audio's DoodleBug, among other products:
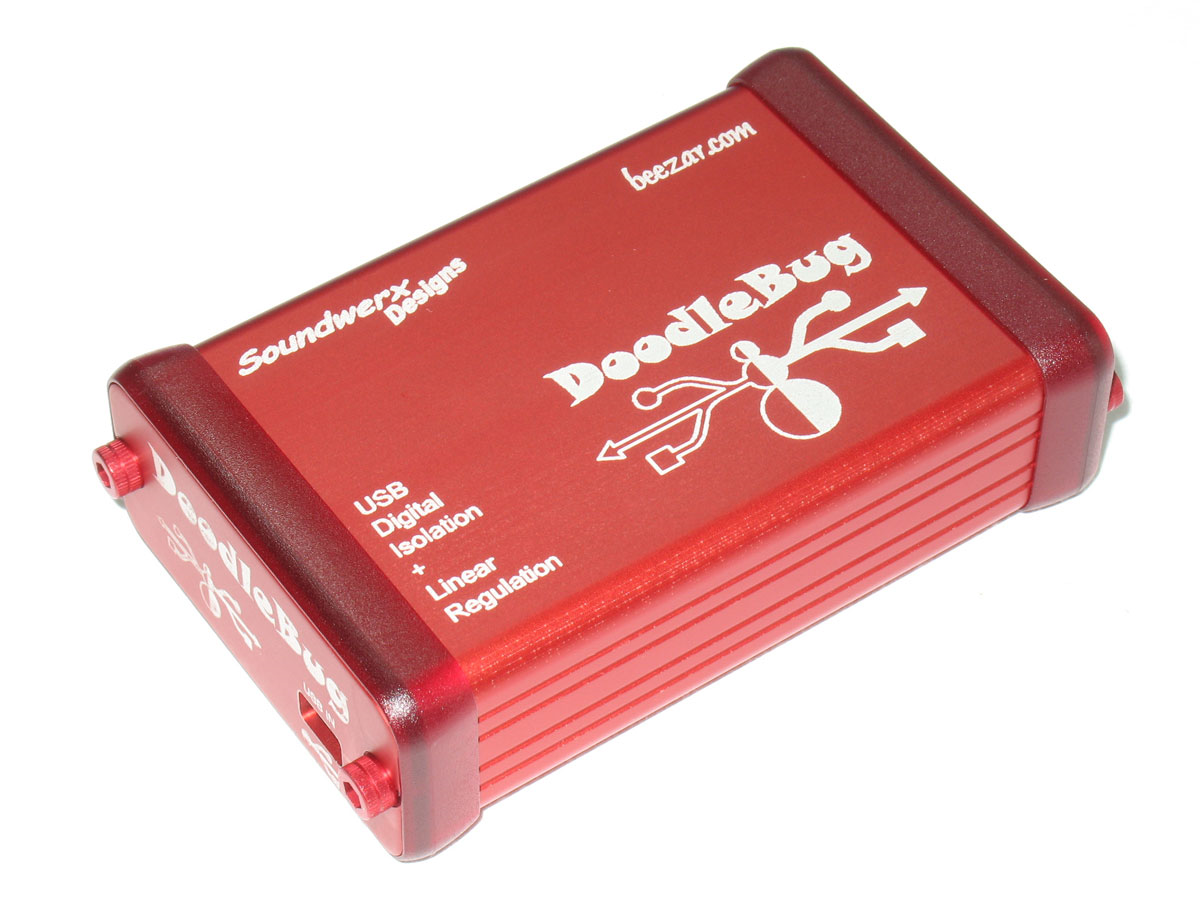
That anodizing is provided by Metal Finishers of Atlanta. The laser-etching is provided by Laser Tech Atlanta. Both firms have done excellent work for me for almost a decade, now. I used to live only a couple of miles from Metal Finishers of Atlanta, so it was very, very convenient. Both services are true crafts, almost artwork. If you look at Laser Tech Atlanta's website, you'll see some fine examples of actual art and why I say that:
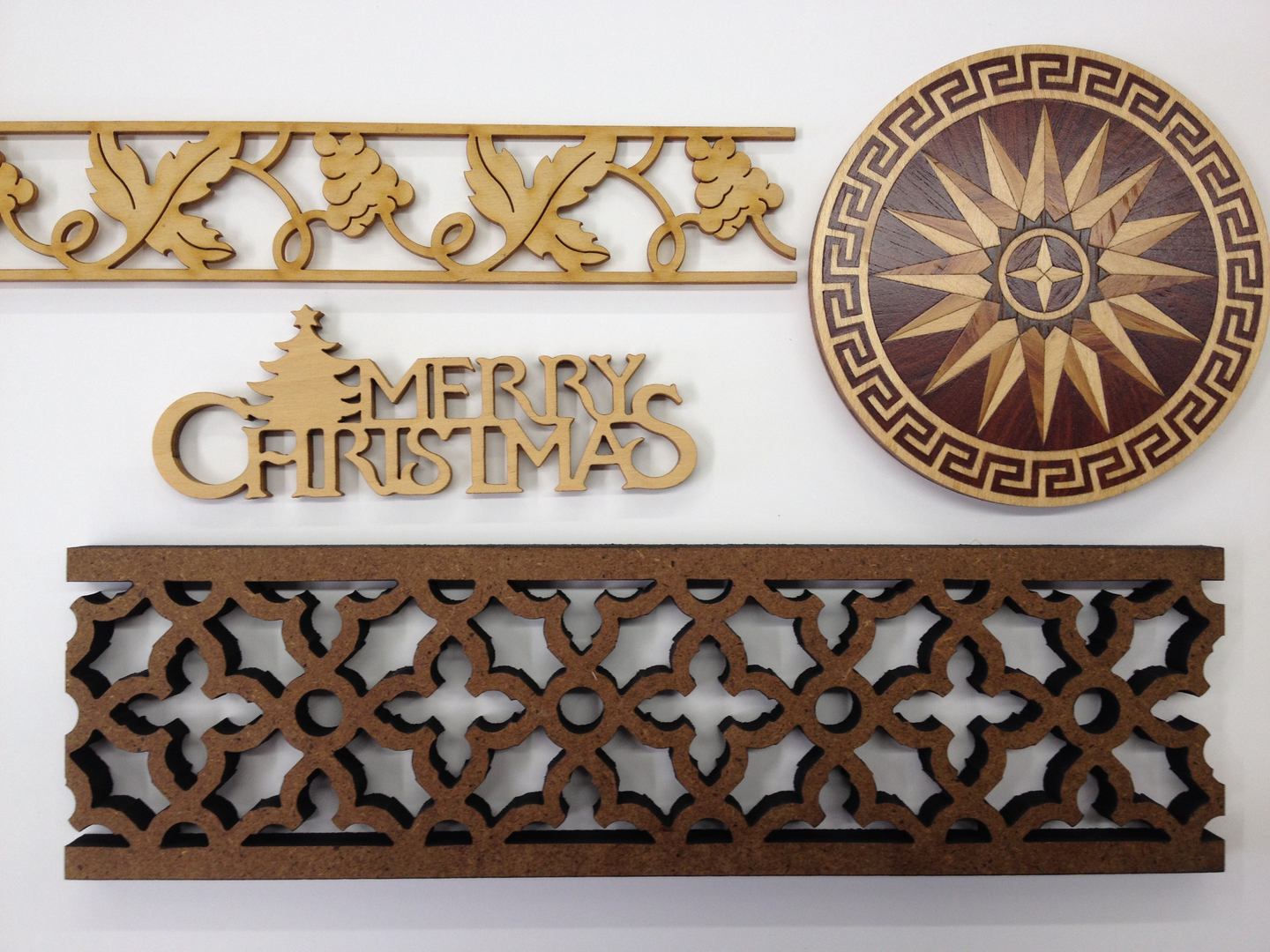
Anodizing is similar: the process is well known and documented, but the actual process details are more experience and judgment than anything else. The type of metal cleaning used, the method of clamping/mounting, and how long to leave the article in each tank during the process, are all variable tasks that can result in huge differences in quality.
Similarly, laser etching not only involves preparation of the artwork, but knowing the various materials and finishes and how to vary the etching settings variables that are necessary to have a design "pop" from the overall finish. It even takes first hand knowledge and experience of the anodizer in the depth of anodizing, etc. Most important - anodizing can actually be done over if it turns out bad, but laser etching cannot. It essentially ruins the metal, if it's not done right. When you've invested several $ thousands in the metal work, failures in anodizing or laser etching are not desirable prospects - to say the least! (I've had it happen, unfortunately!!)
So, all that was in my mind while searching for a solution for the metal. I had to find someone who could precision cut, punch, and brush-finish aluminum to an equal quality of Front Panel Express. Then, I'd have to have it anodized and laser-etched, but at least with those two services - I already had the solution.
After flirting with a number of machinists (my own ignorance), one of them said what I really needed was sheet metal work. Having been familiar with the HVAC industry for many years, "sheet metal work" meant bending thin gauge galvanized steel and assembling it into ductwork with very rough, self-tapping screws:
No! That isn't what I wanted. Yet, another machinist I contacted persisted: he said I needed to look at Swift Atlanta. So, I did.
The first thing I did was call them up and ask if they could machine metal plate and also brush-finish it. By that time, I had actually looked up the actual machines used to brush-finish (Time-Saver) and asked them if they had them - they did! Next thing I knew, they had invited me to their factory for a tour! Even though I had worked for Lockheed in my early career for 15 years, I was impressed with their operation! Giant Mitsubishi laser cutters, presses, Time Saver belt sanders (brush-finishers), CNC press brakes, etc., etc. They did clear anodizing and silk-screening (as good as I've ever seen), but no black anodizing or laser etching. I asked what they did if someone wanted black anodizing and laser-etching: their reply was that they used Metal Finishers of Atlanta and Laser Tech Atlanta! The same people I used! They also stated that they'd handle the entire operation and quality control - including the outside services!
Speaking of the HVAC industry, Swift Atlanta does all of Automated Logic's casework:
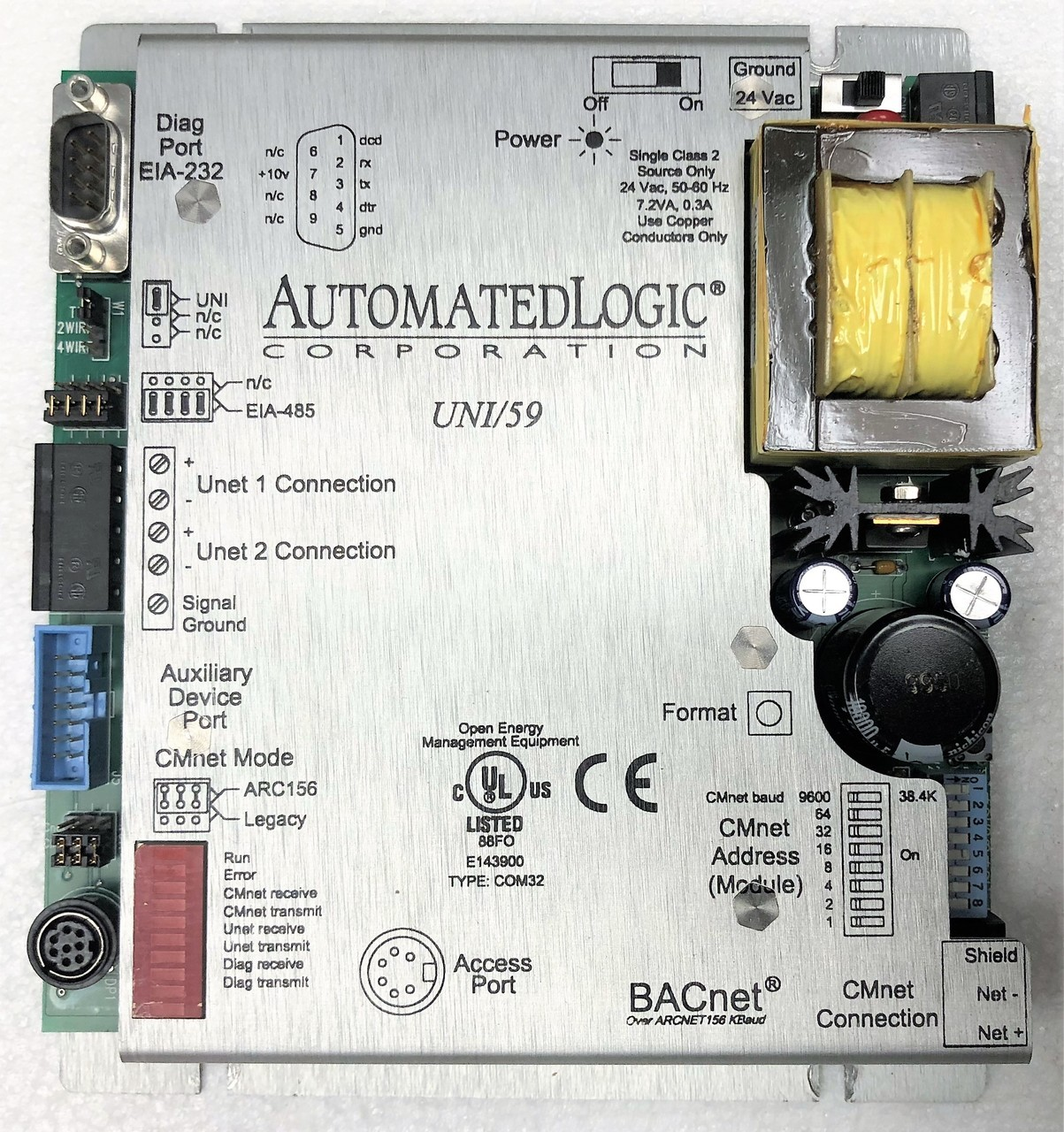
That's not exactly the style of casework we wanted for the T4, but you can see the quality workmanship, regardless.
I had several more meetings with them, showing them the T4 finished prototype and letting them have a look at it, while I produced an entire set of CAD drawings for them. This was a lot of work. Dsavitsk had done the initial work in Front Panel Designer for FPE, but as convenient as their software was, it was not commercial/industrial CAD. I had done this in the past with Lansing on the Millett MiniMAX, Hammond Mfg with the Starving Student, PupDAC, and DoodleBug, and with Context Engineering on the original Torpedo. So while a lot of work, it was something I had done before. Here's a couple of examples of the drawings that I produced:
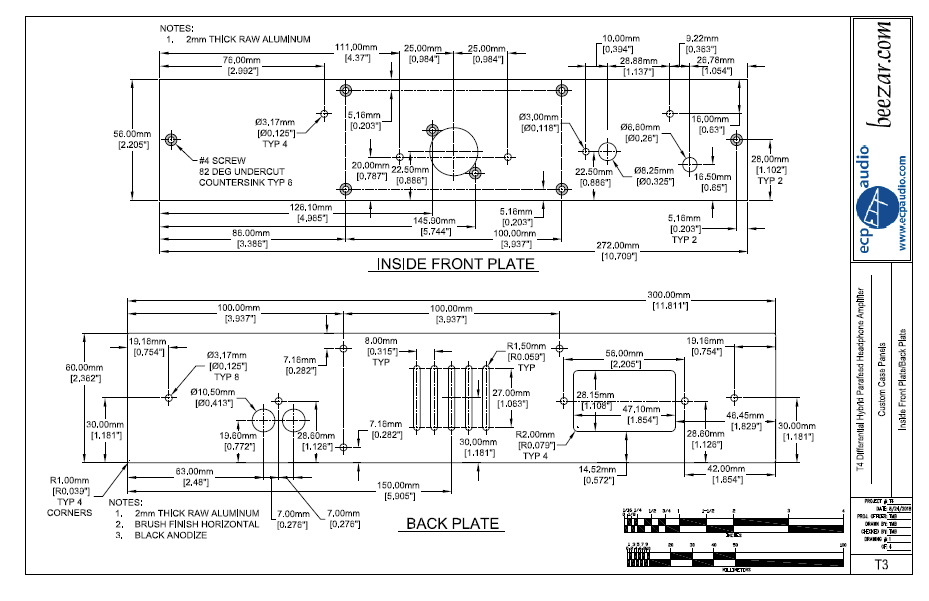
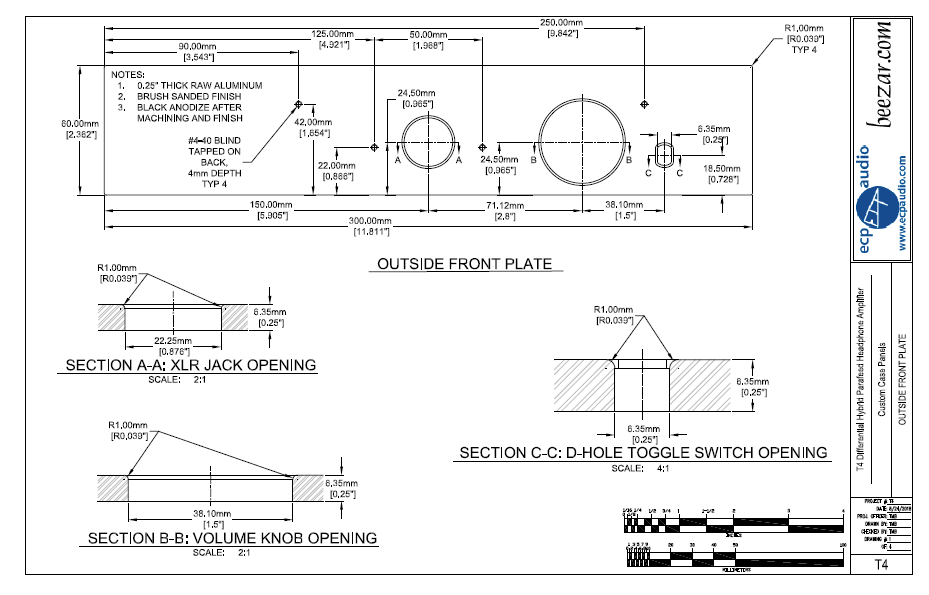
Please remember - I can't take credit for the design! This is Dsavitsk and ECP Audio's creation! I like to think my contribution was definitely value-added, however.
Anyway - I highly recommend Swift Atlanta (and the other two processors) for anyone interested in some high-level casework. My experience with Swift Atlanta was one of the nicest - if not THE nicest - I've ever had with a supplier. They even sent me a Christmas card:
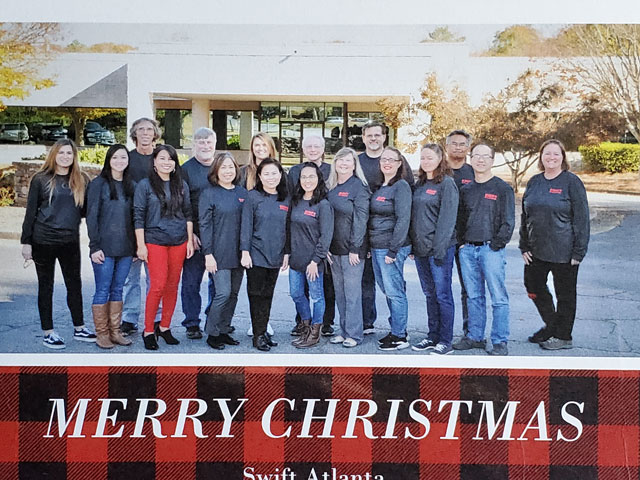
Great people! I just thought some of you would like to know the many people who helped make the T4 possible. It's not just me and Dsavitsk!
Last edited: