aerius
Banned
- Joined
- Oct 14, 2002
- Posts
- 2,365
- Likes
- 26
Quote:
Actually, no, that's too much solder, and you don't have full wetting on a few of the pins, the rightmost pin being the most obvious. The solder should form a smooth concave curve from the pin right to edge of the pad. Instead, you have convex curves that do not have full contact with the pad. Acceptable for consumer electronics, but it will be rejected for medical, automotive, telecommunications, and aerospace/military applications.
Ideally you want a solder joint that looks like the one on the right in the picture below. The solder forms a smooth concave curve and tapers down to nothing at the edge of the pad, full coverage, full wetting.
Here's a cross-section view of what you should be aiming for.
As a general note, guys, go easy on the solder, you don't need that much.
Originally Posted by headchange4u Here's a pic of a corretly soldered LPC pin header on a XBox motherboard (version 1.5). Notice how the solder forms a cone shape. |
Actually, no, that's too much solder, and you don't have full wetting on a few of the pins, the rightmost pin being the most obvious. The solder should form a smooth concave curve from the pin right to edge of the pad. Instead, you have convex curves that do not have full contact with the pad. Acceptable for consumer electronics, but it will be rejected for medical, automotive, telecommunications, and aerospace/military applications.
Ideally you want a solder joint that looks like the one on the right in the picture below. The solder forms a smooth concave curve and tapers down to nothing at the edge of the pad, full coverage, full wetting.
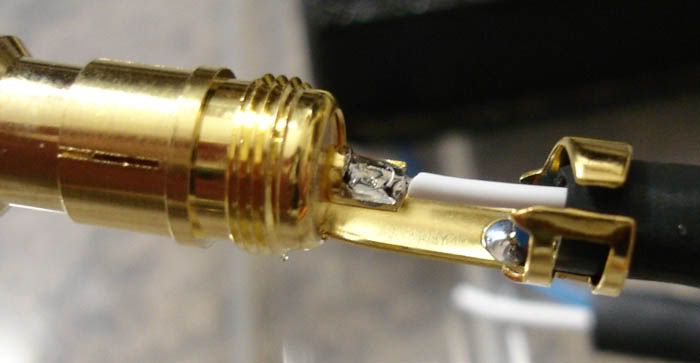
Here's a cross-section view of what you should be aiming for.

As a general note, guys, go easy on the solder, you don't need that much.