jasonb
Headphoneus Supremus
- Joined
- Sep 14, 2010
- Posts
- 5,564
- Likes
- 2,864
Not sure if this is the right sub-forum to post this in, so sorry if it isn't.
Looking for suggestions on the right soldering iron for making a headphone cable. Basically what I want to do is chop up an oem AKG 3.5mm to mini XLR cable and make it shorter, much much shorter. It's going to be for a K371 to a Qudelix 5K which will be attached to the K371.
So the plan is the cut a large section out of the cable, and solder the cable back together, only much shorter and then cover the connection with heat shrink tubing to seal it and strengthen it.
So what would be the type of soldering iron and solder I need for these very small gauge headphone wires?
For picture reference I want to do what's in this picture but hopefully a bit cleaner.
Looking for suggestions on the right soldering iron for making a headphone cable. Basically what I want to do is chop up an oem AKG 3.5mm to mini XLR cable and make it shorter, much much shorter. It's going to be for a K371 to a Qudelix 5K which will be attached to the K371.
So the plan is the cut a large section out of the cable, and solder the cable back together, only much shorter and then cover the connection with heat shrink tubing to seal it and strengthen it.
So what would be the type of soldering iron and solder I need for these very small gauge headphone wires?
For picture reference I want to do what's in this picture but hopefully a bit cleaner.
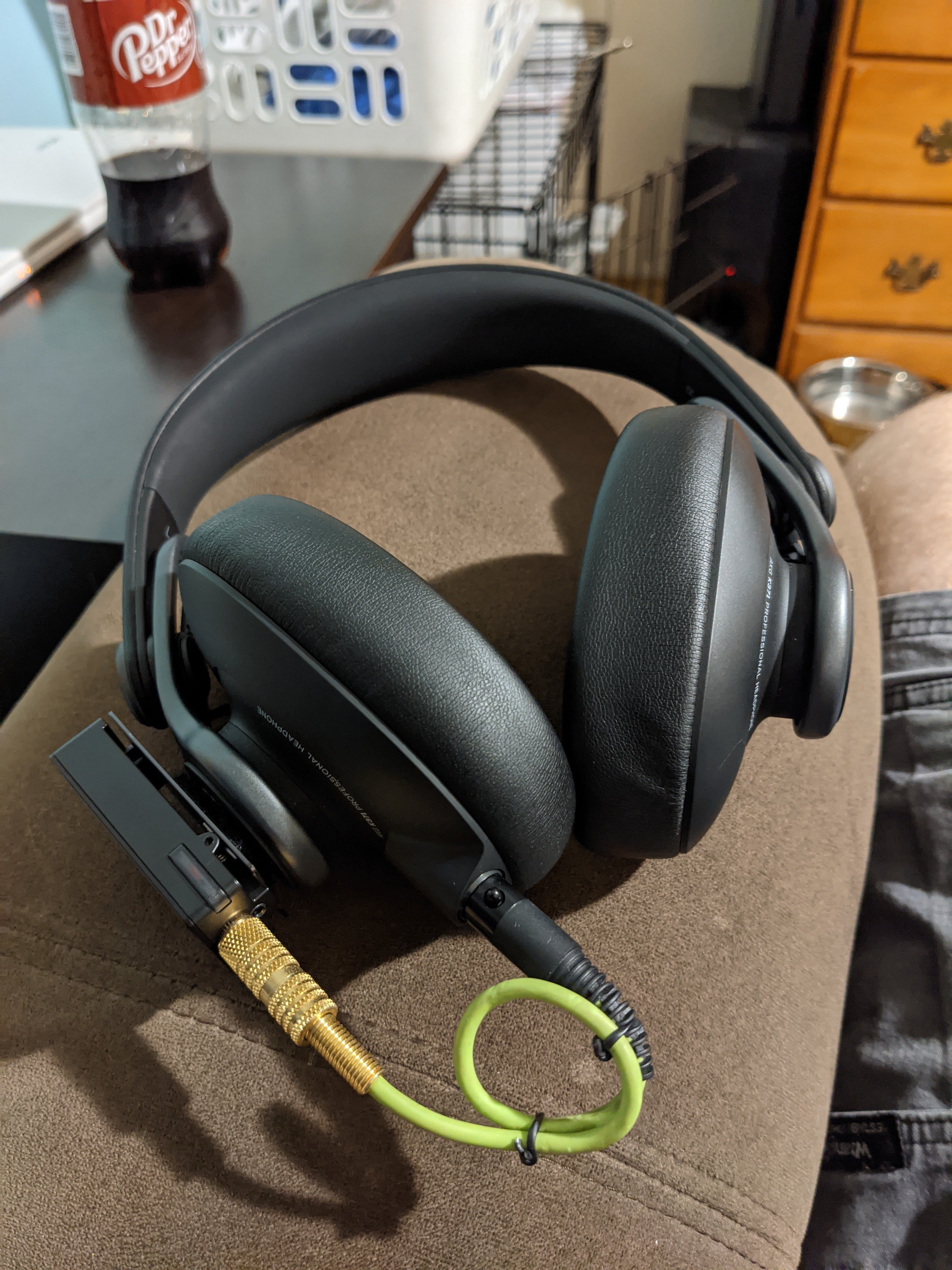